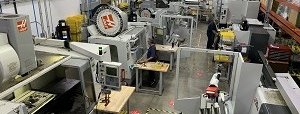
7 Ways Robots can affect your Lean Manufacturing Efforts
Jan 10, 2022
7 Ways Robots can affect your Lean Manufacturing Efforts
Read Time: 1 MInute
Word Count: 255
Key Take Away: Lean manufacturing is whole heartedly embracing robots
- Product quality improvement – Robots allow for consistent production with minimal, if any, defective products. The repetitiveness robots endure allow for increased efficiency on your shop floor.
- Elimination of human limitations during production – A production line’s capacity can sometimes be constrained by human limitations; manual operators can tire or be slowed down by circumstances outside of their own making. This is not an issue with robots.
- Time savings – Robots don’t get tired. By allowing a robot to work continuously, production can complete projects more quickly and efficiently.
- Prevention of health and safety issues – Delegating repetitive, strenuous tasks to robots reduces the risk of health and safety issues (ex., carpal tunnel, joint pain) for CNC machinists and operators.
- Elimination of non-value-added tasks (minimizing waste) – When robotics is implemented into a machine shop, we are forced to evaluate our production process. By doing so, we delegate the repetitive tasks to robots, eliminate the “non-value-added” tasks (such as part preparation, cleaning, etc. by manual operators), and make waste reduction in the production process a priority.
- Automatic “error-proofing” – Advanced software in robotics allows robots to identify when there is an issue in production and notify your production team of the issue.
- Avoidance of wasted human potential – Bouchard notes that humans can contribute in various meaningful ways during production. Forcing employees to focus on loading and unloading of parts is a waste of human potential; having robots take care of the dull, repetitive tasks allows humans to focus on bettering production efforts in a more impactful way