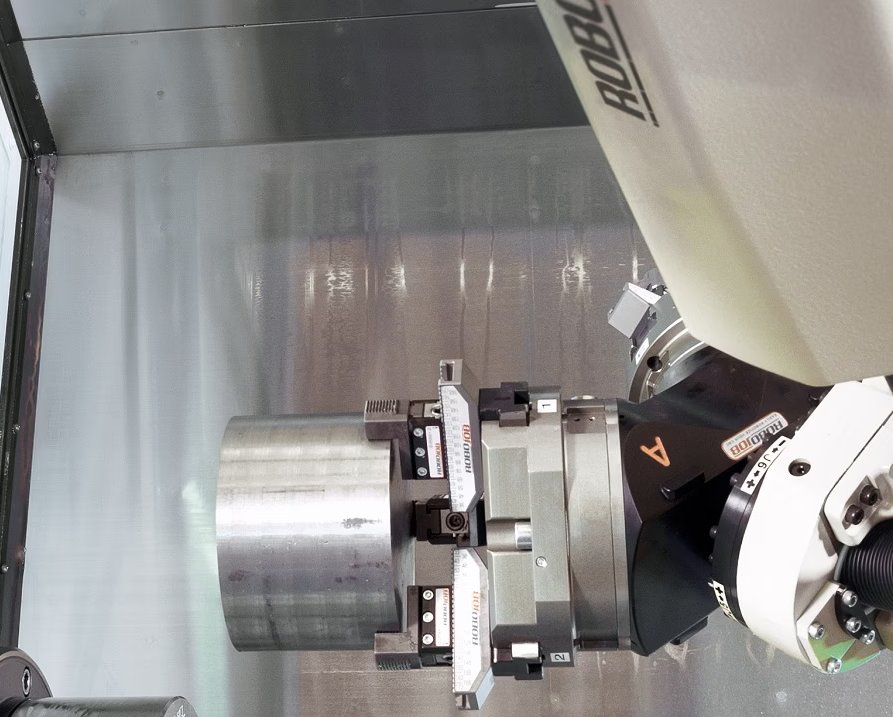
Our Reasons Why You Should Automate Your CNC Machines
In the fast-evolving world of manufacturing, responding quickly to an ever-changing demand is the key to success - and survival. Automation isn’t just a buzzword; it’s a game-changer for CNC operations. From boosting productivity to future-proofing your workforce, automating your CNC machines can transform your business on every level. Curious? Here are some compelling reasons why it’s time to take the leap.