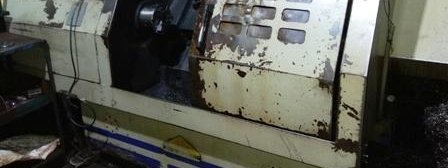
Is My Machine Tool Too Old to Automate?
Is My Machine Tool Too Old to Automate?
Reading Time: 4 Minutes
Word Count: 893
Key Takeaway: Here are 11 things to consider when automating your machine tool.
Is my machine tool too old to automate?
We hear that question a lot. It makes sense. People want to get the most from their machine tools. With an average spindle time of 34%, there is plenty of upside room for production and profits if you can operate that machine tool more frequently.
The answer to the question, “Is my machine tool too old to automate?” is not a simple yes or no.
Any mill or lathe can be updated to become “robot ready.” We see machine tools old enough to be in high school paired with a robot. We see machine tools delivered last week that aren’t robot ready.
CNC automation isn’t simply adding a purpose-built, CNC machine tending robot. CNC automation is a combination of automated processes all working together towards one concrete goal.
This blog post explores ten options to consider when getting your machine tool robot ready. You can do it yourself, have your machine tool vendor do it, or we can do it for you.
We are not as concerned about who does the work as we are about the quality and timing of the completed work. Some of these elements will be obvious even if you’ve never automated a machine tool. Some of these items may be a bit of a surprise.
- CNC operating system. Multiple automation functions work in concert with your machine tool. Your CNC operating system must be able to handle the required functionality. So don’t assume that the current version can handle everything. You’ll want to verify that the OS will handle everything.
- An automatic door opener. Applying a CNC robot to a new or used machine will require a door opener to increase efficiency and minimize operator intervention during production. The last thing you want is the robot opening and closing the door. That is a significant waste of time and resources. Door openers can be pneumatic or servo. If your machine tool has dual doors, you’ll need the opener to open and close both doors.
- Spare M codes. Some machines have available M codes depending on the age of the control and originally purchased options. You should assess if you have these M codes or if spare M functions must be purchased. When verifying that your machine tool OS handles all the functionality, validate that availability to spare M codes.
- Probing. Although not necessary, adding probing to a machine is highly recommended. Probing will allow you to quickly set up parts, reset work coordinates during production, use more universal work-holding that doesn’t require part stops, check parts, apply tool break detection to sensitive tools, and more.
- Automated work-holding. Newer CNC mills have choices for pneumatic, hydraulic, and electric vises. Ask your CNC automation integrator for guidance on the required vise control for older machines. To automate your CNC, an automated work-holding device is imperative.
- Proper work-holding. How you hold parts should be considered when purchasing a robot. Pneumatic, hydraulic, and electric options are available for integration during the automation process.
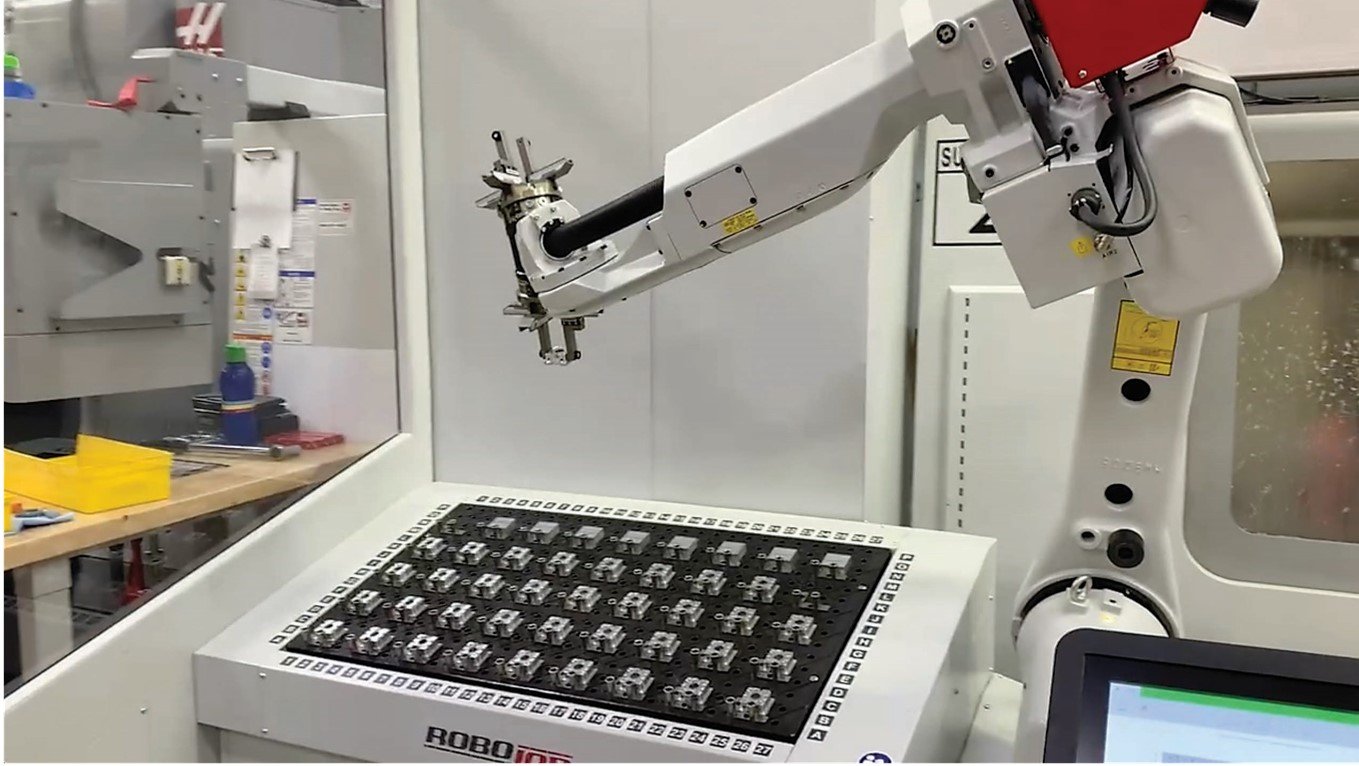
Equipment make: RoboJob-USA
Equipment model: Mill-Assist Essential
CNC machine make: Haas Automation Inc.
CNC machine model: VF-2SS
CNC machine model year: 2008
Shifts per day: one
Shifts per week: five
Productivity increase: 54%
Uninterrupted production time: 13 hours
Total parts produced: 130
7. A chip auger. If you aren’t making chips, you aren’t making money. But extra chips can get in the way of work-holding and cause issues. Chip augers help get chips out of a machine and away from work-holding. This allows production to run smoothly and remain unattended for more extended periods of time. Not having this in place can hobble your production if you are working hard to increase that spindle time
8. A chip-clearing fan. This is a great addition to reduce the coolant and chips on a part as the robot unloads and places the part onto a table.
9. Automated coolant management. This helps production run longer without intervention from an operator and lowers the chance of catastrophic tool failure if coolant runs out or the system becomes clogged.
10. A larger-capacity, side-mount tool changer. Although not required, a larger side-mount tool changer is a handy option to accommodate tools, such as a probe or a chip fan. You also can store redundant tooling in unused pockets and use tool management features to switch to new tools when tooling has reached the end of its life.
11. A fourth-/fifth-axis rotary with a trunnion. A rotary table and a trunnion table can reduce setup times for multiple operations and boost productivity.
Deciding to automate is a crucial investment. We’ve heard many machine shop leaders say that having a robot has gone from being a luxury to a necessity. More and more, the question is not “if” but “when” will you automate?
With proper preparation and the right equipment, CNC automation should reap big rewards. Do not hesitate to ask a trusted, experienced robotic integrator about options to help your shop fully utilize CNC automation.
When you are ready to take the next step in your CNC automation journey, call us at 866-952-9020 and press 1 to start the conversation.