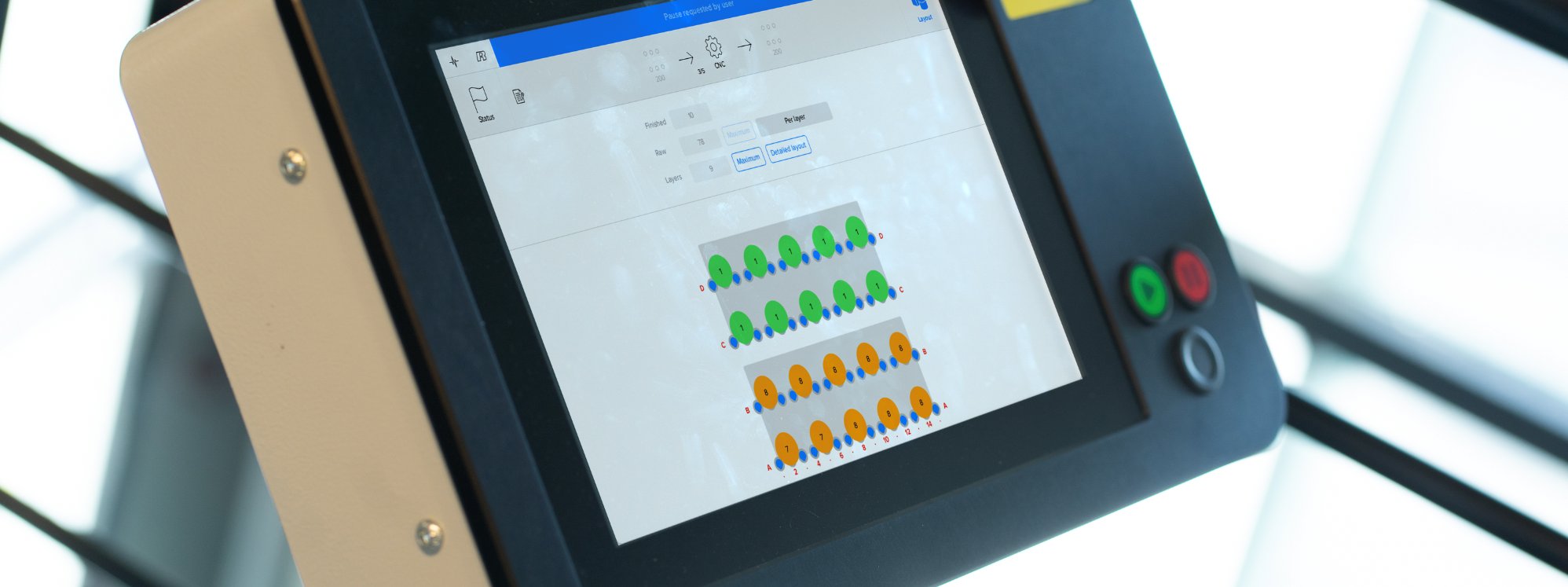
Why Use 20th-Century Software with Your 21st-Century Machine Tool?
Why Use 20th-Century Software with Your 21st-Century Machine Tool?
Reading Time: 4 minutes
Word Count: 1146
Key Takeaway: It took nearly 30 years, but the CNC machine changed the face of machine shops.
During the late 1940s, James Parsons was a computer pioneer who worked for the Air Force. Some credit Parsons as the father of the CNC machine.
Others credit Richard Kegg, who worked for Cincinnati Milacron. In conjunction with MIT, Kegg created the first CNC milling machine. That was in 1952; in 1958, Kegg was awarded the patent for this milling machine. That was the first positioning machine tool.
In the late 1960s and early 1970s, Computer-Aided Design (CAD and Computer Aided Machining (CAM) developed. It is hard to overestimate the impact CAD-CAM software had on machining. That was absolutely a game-changer. Can you imagine trying to get things done without that software today?
It was in the late 1980s that CNC machines became widely accepted.
Over the last 30 years, your CNC software has made impressive strides. Each software version changes the CNC machine capabilities where it resides.
I listened to two CNC machine representatives discuss changes in their latest operating software release. It was a fascinating lesson on the changes in CNC operating systems.
Some of the discussion was about the simple things we take for granted, like an automatic door opener. The software enables that function.
As they compared and contrasted the old and new versions, their level of knowledge about the new release was impressive. It was clear that these two knew their product exceptionally well.
I was even more impressed with their knowledge of customers, their needs, and how the latest release would help the customer base. They even identified specific customers and the types of parts they produced. They tied features to different customers and the benefits the customers would see.
Then the conversation took an unexpected turn. I still needed to look at it from the rep's perspective. One of the reps was struggling with the question and asked, "why would someone use 20th-century software with their CNC?
Even though I was more of a listener than a participant, I asked him, "What do you mean?"
He explained that their latest release improved the robot/CNC interface.
Despite that, people still haven't added a robot to tend their CNC.
Then he added, "Using a machine operator is like using 20th-century software to run a 21st-century CNC. You aren't getting nearly the same level of productivity out of your machine tool without a robot. The robot gets every ounce of productivity from the machine tool. The machine operator? Not so much. The difference between the two is dramatic. I don't get it. Why wouldn't you want to use the robot to get the most from your machine tool?"
I wish I had the answer.
I suspect it is like a lot of things.
People were hesitant to adopt the CNC machine at first. The CNC machine required another skill set than using their old Bridgeport. New skill sets take time to develop. It can be challenging to find the right people when skills are changing.
When the pain of remaining the same is greater than the pain of change, psychologists say people change. Otherwise, habit is pleasurable. After all, people park in the same spot in the parking lot even without assigned parking spaces.
Slowly adapting to change was the same as in the early 1980s. Habits can be hard to break and change.
The CNC patent had been around for 25 years, but people still hung on to their human-powered lathes and mills. They didn't want to change. When they first started losing business to machine shops with CNC machines, they didn't change. They got serious and prepared for change when the losses became more dramatic.
They took the plunge, bought a CNC machine, and learned to use it. Then a funny thing happened. Once they purchased one, they bought another, and another, and another.
Once they switched, they couldn't imagine going back.
The only question they seemed to ask was, "why didn't I do this sooner?"
All those other questions they asked before the change seemed to go away.
What were those questions?
- "Why should I use one of those machines?"
- "What about the people?"
- "I've always done it this way; why should I change?"
Those questions had the same answer: "There is nothing wrong with what they were doing. They just weren't ready yet. And that's OK."
We know that machine shop leaders are intelligent people. The machine shop universe is easier to survive if you are smart. Even then, being a brainiac is no guarantee of success.
Machine shops go under when the economy is booming, and machine shops thrive when the economy is bumpy. It isn't about the economic conditions. It is about leadership decisions.
Robots are much like the CNC machines of the late 1980s. People may want to avoid making the plunge. There can be some uncertainty around technology. No one wants to be held captive by technology.
That is why we've worked to take the complexity out of robots for more than fifteen years. Our customers want to run their businesses, not be held captive by complicated technology.
Machine shop leaders don't want things that take their focus away from customers and business operations.
That is why we designed our robots to make technology as simple as possible. There is no programming. You enter raw and finished parts dimensions along with the material and the piece count.
Need OP10 or OP20? You add that with a drag-and-drop function. The whole thing only takes 5 minutes.
We know machine shop leaders want to avoid having their bottom line held captive by expensive annual maintenance agreements or having a robotic engineer on site.
Our annual maintenance? Four C-Size batteries once a year. That keeps the clock and the robot positioning calibration in place.
That robotics engineer? You don't need them. The robots rarely have an issue; when they do, our engineers jump in and take care of it. More than 92% of the time, they solve the case over the phone.
Once in a while, we have to get on-site to assess the root cause of the issue further. We do that quickly. We understand that you want to be making chips all the time. You don't need unplanned outages.
Whether it takes six months or six years, just like machine shops will be adding robots, without that robot, it is like using an old Bridgeport to compete against the latest CNC machine.
We are here for you when you are ready to discover how our robots can help your machine shop control costs, boost production, and improve profitability.