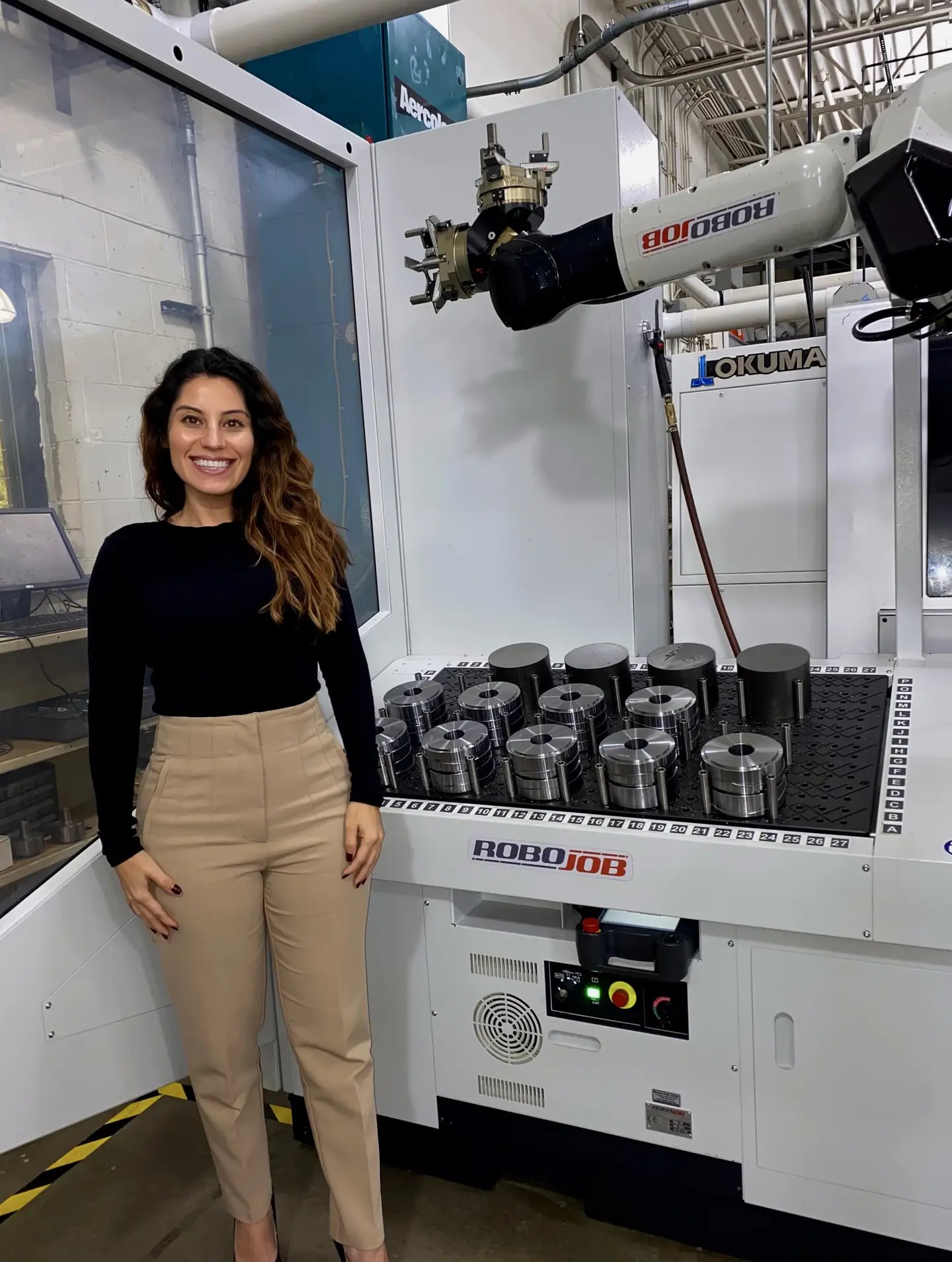
HM Manufacturing
HM Manufacturing
HM Manufacturing Amplifies Success With CNC Automation from RoboJob!
Craig Zoberis sat down with Nicole Wolter of HM Manufacturing to discuss automating her machine shop.
CZ: Why are you automating your machine shop now?
NW: If we're being honest, I wanted to automate four years ago, but I had an old-school dad who thought that you couldn't do automation with a high-mix, low-volume scenario. It was great that we were able to prove him wrong just recently and so, I think if you don't do it, you're missing out and going to be left behind because everyone is doing it. I'm looking to try to get another one soon because we're quoting things that we need that for, and as we all know, we can't find the people, so if you can't find the people, you have to find another solution, and automation is the key.
CZ: Now that you have a RoboJob system installed, what did you discover now that you didn't know before?
NW: I think the ease of being able to program it and use it. There's this huge stigma that automation is cumbersome; it takes a lot of time to program, it takes a lot of time to set up, and if you're not doing tens of thousands of parts, it's not useful. Now that we have it and have been using it, the programming is super easy; the setup is super easy. We can do it in minutes and so that’s great when you have a lot of different parts that you must run.
CZ: Now with it installed, what did your team discover?
NW: I do have a very young crew, so it's different for me, I don't have to change anyone's mindset because they do think automation and robotics is needed today, plus they all want to be involved with it, be able to set it up and be able to run it.
CZ: As you know, people don't realize that machinists are artists. They're doing precision machining, but they're being creative in the work on how they machine the parts, how they hold the parts, how they fixture the parts. How they can move it from doing a 16-minute cycle to a 12-minute cycle whatever it might be. Now, we're taking out that repetitive task. Do you see there's an opportunity? I know you've had it in there for a while now, but have you seen any cultural shift towards the management showing that they're interested in them being more creative rather than being tasked with an operation of machine tending?
NW: So, yes, I've had my CNC lathe operators now want to go to Mastercam to learn at a higher level. So, they want to do the 3D, they want to do the level 2, the level 3, because they're looking more now to advance their skill set, whereas before they thought that maybe it was just kind of a button pusher situation. So now they've actually come to me and be like "hey, now that we're doing more of these precision parts for Aerospace Defense, which is super creative on the gearing side, the shaft side, there's a lot more to it, they're looking to advance their skill set and they're trying to see if they can run other machines like an ODID grinder which takes a different skill set, so now that they have more time, they're looking to see what else they can do and I think that that's super important.
CZ: So, this a good retention factor. If you have the robot doing the repetitive work, they're focused on the creative and learning side of things, it's going to keep them working at HM Manufacturing. Also, it can be an attraction feature too for new talent as well, if you show that you don't have to do the monotonous, you can do the creative work, I believe that is going to help you. I know you're very good at recruiting, especially young talent, so tell me more about in that arena how that's going to affect things for you.
NW: So, if you have more automation on your floor, they can use their talents and skillsets. A lot of these kids coming out of high school already have some manufacturing background, and they're not on manual Bridgeport mills, and they're not on manual lathes anymore, they're on CNC equipment. So, the worst thing you can do is attract this new talent and have them sit there and do nothing advanced. If they can start programing and doing more of that higher level skill work and be involved with the automation and robotics, I think that's the best thing you can do, not just for retention, but to keep manufacturing a cool career to choose.